La stampa 3D sta conquistando sempre nuove applicazioni industriali e non, grazie all’evoluzione di tecnologie, materiali e finiture
Innovazione ed evoluzione. Sono i due cardini su cui si basa la ricerca di nuove possibilità di espressione nei diversi campi che compongono la nostra vita di tutti i giorni. Ed è una evoluzione che è sempre più veloce. Pensiamo ai telefoni cellulari. Non più di 20 anni fa avere un telefono cellulare era una cosa da pochi, uno strumento che svolgeva una funzione, telefonare. Oggi il cellulare è parte integrante della nostra vita, quasi indispensabile, perché in esso sono concentrate praticamente tutte le funzioni che ci servono per relazionarci, lavorare, svagarci, gestire. In 20 anni tutto è cambiato. Incredibile vero? Si, ma in realtà l’innovazione viaggia a una velocità sempre maggiore, spinta non solo dalla soddisfazione di un bisogno ma dalla volontà di cambiare le nostre abitudini e rendere le cose più semplici. Un esempio di questa accelerazione lo vediamo in molti settori, dai trasporti alla produzione di energia, dalle telecomunicazioni alla produzione industriale. E forse spinta da questa domanda di modernizzazione, la stampa additiva, o come viene spesso chiamata stampa 3D, è sicuramente uno dei settori di ricerca che in pochi anni ha saputo crescere in modo esponenziale, trovando applicazione, e in alcuni casi inventando l’applicazione, in molti ambiti di utilizzo. Se pensiamo alla stampa 3D la prima cosa che viene in mente è un pupazzo, che sia una miniatura da collezione o una “scultura” di grandi dimensioni che ci accoglie fuori da un ristorante, in un parco divertimenti, nella vetrina di un negozio. Un po’ come per il telefono: tutti sanno che serve a telefonare, e quindi non sorprende vederlo usare per questo scopo, ma in realtà è solo la punta di un iceberg. Componenti meccaniche, usi in medicina e nel campo delle protesi, prototipazione, oggetti di design, arredo urbano, componentistica. Ogni settore usa la stampa additiva, e sempre di più sta diventando una risorsa.
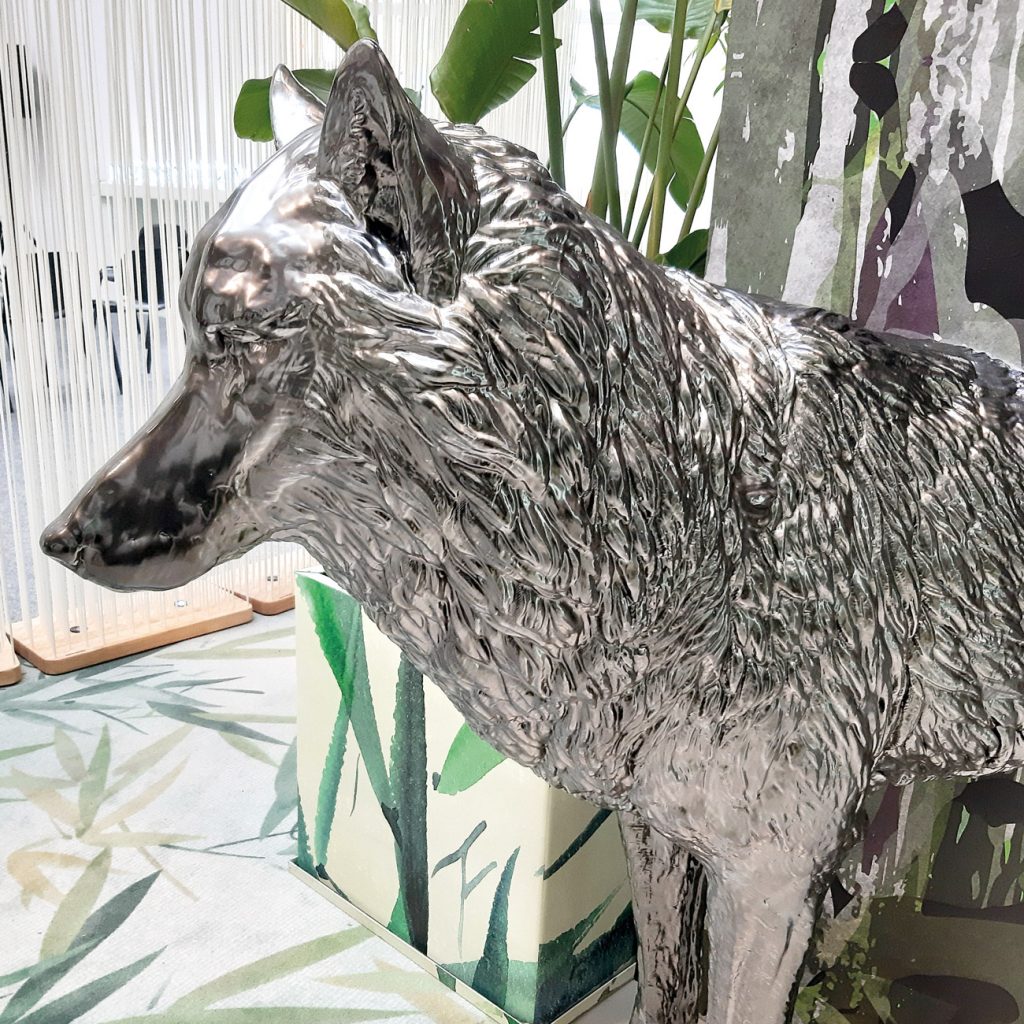
Ma vediamo, brevemente, esattamente cosa si intende per stampa additiva. A differenza della stampa 3D, che viene ricavata sia per aggiunta di materiale che per sottrazione, al fine di ottenere un oggetto tridimensionale, la stampa additiva riunisce tutte quelle tecnologie che depositano un materiale o polimerizzano un materiale, creando un oggetto a 3 dimensioni. Le più diffuse, soprattutto non nel mondo professionale e industriale, sono i sistemi che depositano un filamento di materiale plastico che viene indurato con l’uso di lampade UV, e strato dopo strato determinano la forma e il volume dell’oggetto. Ma esistono molte altre tipologie, che usano anche materiali quali metalli e materiali non plastici. A monte del processo di produzione c’è naturalmente l’elaborazione di un file con appositi software, a valle tutta una serie di tecniche di finitura. Non ci occuperemo in questa sede di questi passaggi e ci concentriamo sulle tecnologie di produzione.
Le tecnologie
Sinterizzazione Laser Selettiva
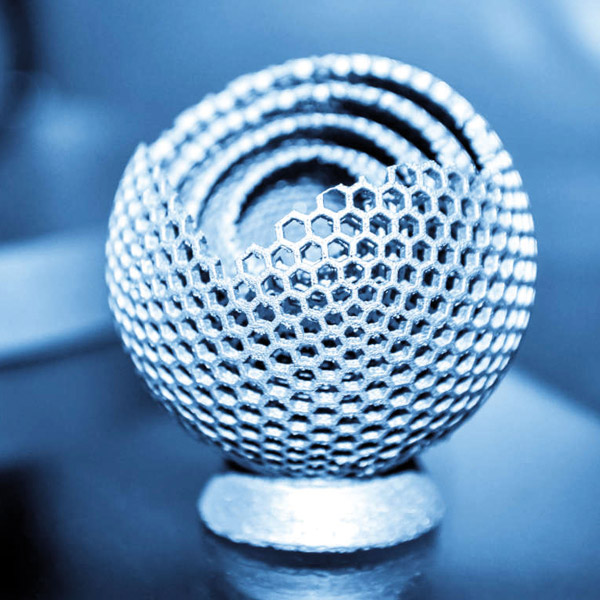
La sinterizzazione laser, denominata anche sinterizzazione laser selettiva (SLS), è una delle tecnologie di stampa 3D più versatili e più frequentemente utilizzate: parti stampate con sinterizzazione laser si trovano ad esempio negli aeroplani, nei prodotti indossabili, in componenti di macchinari e attrezzi di produzione.
Dal momento che non richiede strutture di supporto, questa tecnologia è idonea per parti interdipendenti, parti mobili, cerniere integrate e altri progetti altamente complessi. Sia per i prototipi completamente funzionali sia per la produzione in serie di parti complesse destinate all’utilizzo finale, la libertà progettuale offerta dalla sinterizzazione laser rappresenta la soluzione ideale.
I materiali utilizzati nella SLS sono sostanzialmente polveri e materiali a base Poliammide, sia puri che in combinazione ad esempio con alluminio o vetro, e Polipropilene.
Modellazione a deposizione fusa (FDM)
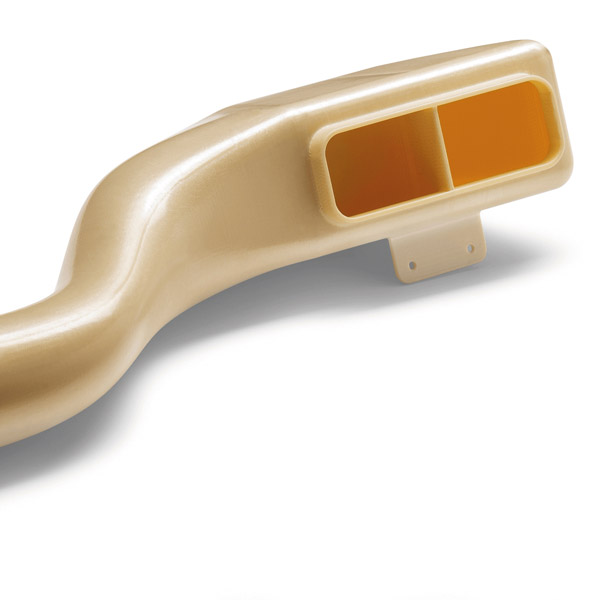
Con la tecnologia FDM è possibile realizzare virtualmente ogni geometria si abbia in mente. Per questo motivo è possibile trovare parti stampate in FDM come componenti destinati all’utilizzo finale negli aeroplani, come attrezzi di produzione in uno stabilimento automobilistico e come prototipi praticamente ovunque. La tecnologia FDM si basa sull’uso di un filamento dal quale una testina a temperatura controllata estrude, strato dopo strato, un materiale termoplastico sulla piattaforma di produzione. Ove necessario, viene creata una struttura di supporto, costruita con un materiale solubile in acqua. Uno dei maggiori vantaggi della tecnologia FDM è rappresentato dai materiali durevoli impiegati, dalla stabilità nel tempo delle loro proprietà meccaniche e dalla qualità delle parti prodotte. I materiali in termoplastica di produzione usati nell’FDM sono adatti per prototipi funzionali dettagliati, strumenti di produzione durevoli e per la produzione di parti in volumi limitati.
I materiali utilizzati sono ABS e Policarbonato, puri o miscelati tra loro, Ultem.
Stampa 3D in metallo
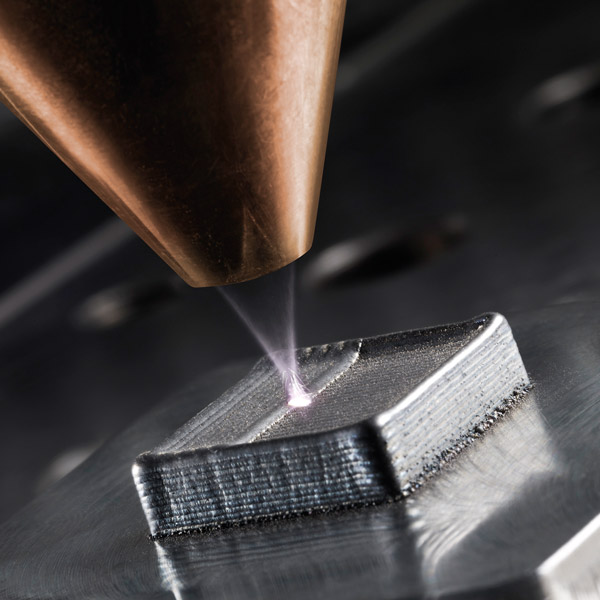
La stampa 3D in metallo si colloca in una posizione particolare nell’attuale sviluppo di prodotti. Permette la produzione diretta di parti complesse destinate all’utilizzo finale e facilita la realizzazione di utensileria per le tecnologie di produzione convenzionali, riducendo i costi e i tempi di consegna. Questa tecnologia è detta anche sinterizzazione laser diretta di metalli (DMLS) e fusione laser selettiva (SLM). La stampa 3D in metallo è una tecnologia laser che impiega metalli in polvere. Analogamente a quanto avviene nella sinterizzazione laser, le particelle sul letto di polvere vengono legate selettivamente tra loro mediante un fascio laser ad alta potenza, mentre la macchina distribuisce strati sottili di polvere metallica. Le strutture di supporto vengono generate e costruite simultaneamente utilizzando lo stesso materiale e vengono in seguito rimosse manualmente. Una volta completata, la parte viene sottoposta a trattamento termico.
Questa tecnologia combina la flessibilità nel design offerta dalla stampa in 3D e le proprietà meccaniche del metallo. Dagli inserti per attrezzi dotati di canali di raffreddamento alle strutture leggere per il settore aerospaziale: ogni applicazione che comprende parti complesse in metallo può sfruttare tutti i vantaggi offerti dalla stampa 3D in metallo.
Tra i materiali utilizzati il Titanio, l’alluminio, acciao inox.

ELMEC 3D per AVI.COOP
Dare “nuova vita” a un macchinario industriale desueto, offrendo la propria expertise a servizio dell’industria alimentare. È quanto ha fatto di recente Elmec 3D per AVI.COOP. L’azienda, con sede a Cesena e parte del sistema Amadori, si è rivolta alla manifattura additiva e, nello specifico, a Elmec 3D per realizzare una mano di presa per braccio meccanico andato fuori produzione, migliorando ulteriormente velocità e prestazioni del robot.
Il progetto, a cura di Elmec 3D, ha visto in una prima fase la riproduzione del componente originale tramite tecnologia Multi Jet Fusion di HP, comportando già un primo alleggerimento e una riduzione dei costi di produzione.
Dopo una fase di ottimizzazione, il risultato è stato una nuova mano di presa dal peso dimezzato e dal costo di produzione ridotto del 97%, con conseguenti vantaggi in termini di performance del robot e della catena di produzione.
Stampa 3D a base di polvere, senza laser
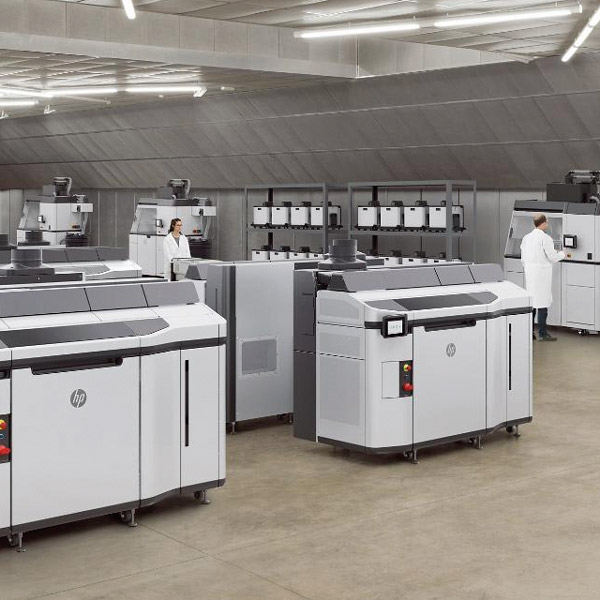
HP Multi Jet Fusion è una tecnologia basata su polveri, che però non impiega i laser. Il letto di polvere viene riscaldato all’inizio in modo uniforme. Viene poi depositato un agente di fusione nei punti in cui è necessario fondere selettivamente le particelle; un agente di rifinitura viene depositato intorno ai contorni, per migliorare la risoluzione delle parti. Mentre le lampade passano al di sopra della superficie del letto di polvere, il materiale depositato cattura il calore e contribuisce a distribuirlo in modo uniforme.
Multi Jet Fusion impiega materiali a grana fine, con i quali è possibile realizzare strati ultrasottili da 80 micron. In questo modo, le parti realizzate presentano una densità elevata e una bassa porosità rispetto alle parti in PA 12 prodotte con la sinterizzazione laser. Inoltre, la superficie si presenta eccezionalmente liscia già al momento dell’uscita dalla stampante e pertanto le parti funzionali richiedono una finitura minima in post-produzione. Tutto ciò si traduce in tempi di consegna rapidi, ideali per i prototipi funzionali e per le piccole serie di componenti finali.
Questa tecnologia utilizza materiali quali poliuretano termoplastico e poliammide.
PolyJet
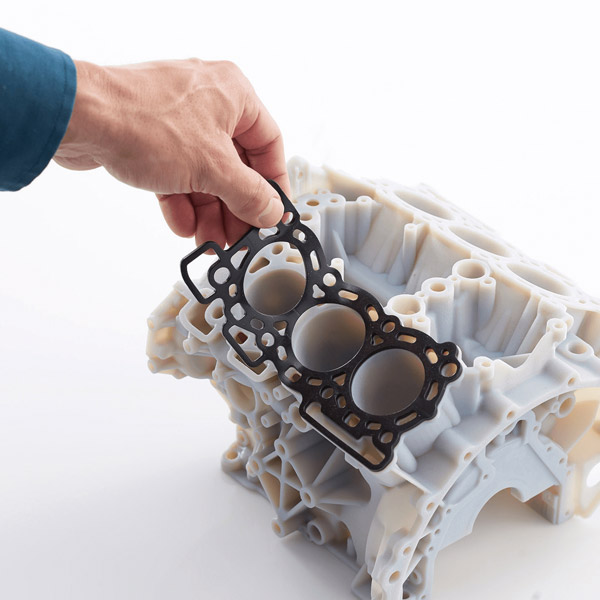
Talvolta, usare un materiale per volta semplicemente non basta. PolyJet offre la possibilità, davvero unica, di stampare parti e insiemi realizzati in più materiali, con proprietà meccaniche e fisiche differenti, il tutto in un singolo processo di produzione. In questo modo, potrai ordinare senza problemi parti di complessità mai vista, composti utilizzando più materiali e colori, con la finitura di un prodotto finale di alta qualità. PolyJet funziona depositando getti di materiali fotopolimerici, in strati ultrasottili, su una piattaforma di produzione. Ogni strato di fotopolimero viene vulcanizzato mediante luce UV immediatamente dopo essere stato depositato, producendo modelli completamente vulcanizzati che possono essere manipolati e utilizzati immediatamente, senza che sia necessaria la postpolimerizzazione. Il materiale di supporto simile a un gel, progettato per sostenere geometrie complicate, viene successivamente rimosso a getto d’acqua.
La tecnologia PolyJet permette di creare strati orizzontali di appena 16 µm (0,0006”), dettagli precisi e pareti ultrasottili fino a 0,6 mm (0,024”) in funzione della geometria della parte. Questo significa che PolyJet permette di costruire componenti meccanici estremamente precisi, offrendoti prototipi di alta qualità per ridurre i tempi di immissione sul mercato.
Colata sotto vuoto
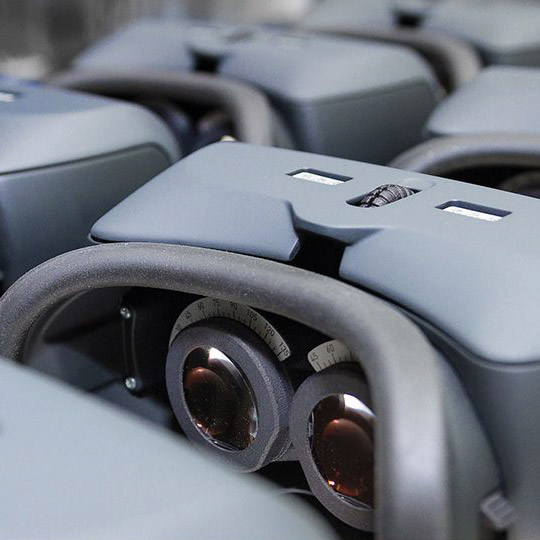
La colata sottovuoto è una tecnica di replicazione impiegata per la produzione di piccole serie di parti funzionali in plastica. La colata sottovuoto, che impiega poliuretani bicomponenti e stampi in silicone, è nota per la rapidità con cui permette di produrre prototipi di alta qualità o prodotti destinati all’utilizzo finale.
La Colata sottovuoto ha inizio con la produzione di un modello master, in genere tramite stereolitografia o sinterizzazione laser, con una finitura di alta qualità superficiale. Viene poi prodotto uno stampo in silicone, mediante colatura del silicone intorno al pezzo master; questa operazione viene eseguita parzialmente sotto vuoto, per evitare la formazione di bolle d’aria. Dopo la vulcanizzazione, lo stampo in silicone viene tagliato secondo piani di apertura predefiniti e il master viene rimosso, lasciando una cavità che permette di eseguire le copie. Lo stampaggio in silicone permette di ottenere parti di alta qualità, paragonabili ai componenti realizzati con stampaggio a iniezione. Questa tecnologia permette di ottenere modelli colati sotto vuoto particolarmente idonei per test di forma e funzione, per le attività di marketing o per una serie di parti finali in quantità limitata. La colata sottovuoto, inoltre, si presta particolarmente a diversi gradi di finitura, per questo siamo in grado di abbinare a questa tecnica la finitura che desideri per le tue parti.
I materiali sono poliuretano, PP, ABS e PC.
TetraShell
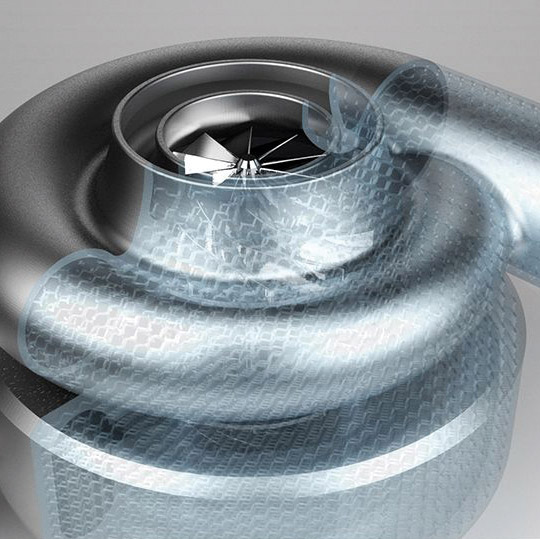
TetraShell è un processo che permette di creare mediante stereolitografia un modello estremamente leggero, che viene poi utilizzato in fonderia per realizzare un guscio di ceramica per la colata in metallo. Il software TetraShell converte il file del modello 3D di un solido in un modello cavo, composto da un guscio esterno molto sottile e rinforzato internamente con una struttura a tetraedro. La struttura interna ultra leggera impedisce al guscio di ceramica di subire danni a causa dell’espansione termica.
Costruire modelli per fusione a cera persa in un unico pezzo permette di ottenere una maggiore accuratezza dimensionale e una migliore ripetibilità, oltre a ridurre il rischio di difetti superficiali come le inclusioni. Le nostre macchine brevettate per stereolitografia Mammoth ci permettono di costruire modelli con una lunghezza fino a 2,1 metri, con la migliore finitura di superficie nella loro categoria. Con uno stabilimento completamente attrezzato per la stereolitografia e un’unità di post-produzione dedicata, la nostra elevata capacità ci permette di offrire tempi di consegna competitivi per i tuoi modelli stampati in 3D. Come materiale viene usato TuskXC2700T, un materiale trasparente con un leggero riflesso azzurro idoneo per numerosi livelli di finitura definita. La trasparenza di questo materiale assicura il completo drenaggio dei residui di resina per una migliore qualità della fusione.
Una nuova tecnologia 3D
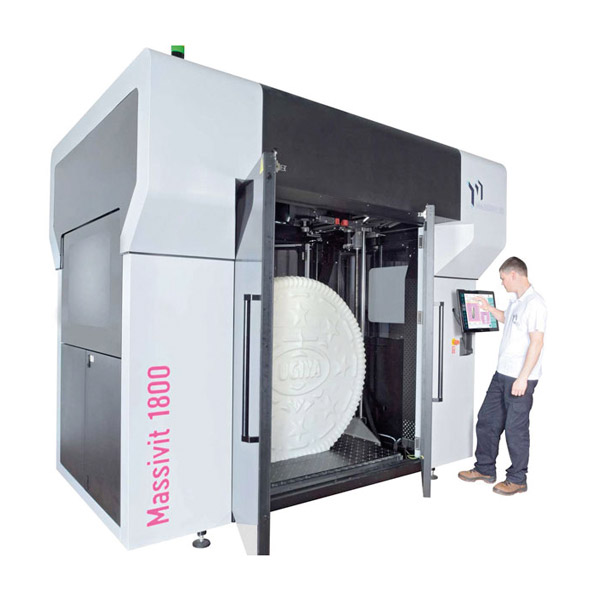
Massivit 3D, azienda israeliana, offre una soluzione completa di hardware, software e materiali di consumo che permette alle aziende di stampare oggetti in 3D di grandi dimensioni (fino a 180Hx150Lx120P cm) e a grande velocità. Una grande opportunità per gli stampatori digitali di grande formato e per i produttori di espositori per la grande distribuzione oltre che ad applicazioni di scenografia teatrale e televisiva. Il cuore di questa soluzione è la tecnologia GDP, il materiale di stampa Dimengel Massivit. Una tecnologia unica basata sul Massivit ‘Gel Dispensing Printing’ (GDP) che non esiste su altri sistemi di stampa 3D. Questo gel a polimerizzazione UV consente al sistema di stampa Massivit 3D, di costruire oggetti ad alta velocità rispetto a qualsiasi altro sistema attualmente sul mercato e consente inoltre di risparmiare una notevole quantità di materiale senza l’aiuto di sostegni, salvo rari casi. Per questo Massivit permette di stampare oggetti di dimensioni più grandi con una velocità superiore a qualsiasi sistema di stampa 3D oggi sul mercato. Massivit 3D è in grado di stampare fino a 35 cm di altezza all’ora. Il tempo di stampa, dipende ovviamente dalle dimensioni e dalla forma o complessità dell’oggetto: per esempio impiega circa 5 ore per stampare la scultura di un essere umano in piedi (‘Adamo’) in dimensioni reali, e la stampante può essere utilizzata nello stesso tempo di stampare in contemporanea anche un altro oggetto (magari Eva). GDP – Gel Dispensing Printing, consiste in una nuova tecnologia digitale. Il processo GDP è completamente diverso dai sistemi di stampa 3D a incandescenza, in quanto utilizza un movimento simile a quello usato nei sistemi FDM (Fused Deposition Modeling) modellazione a deposizione fusa. Durante l’utilizzo del Dimengel – un materiale sensibile alla luce UV – polimerizza e si indurisce mentre viene stampato ed esposto alla luce UV. In questo modo si stampano sottili strati con movimenti lineari di stesa del materiale fino a 1 metro al secondo. Nel complesso, la tecnologia Massivit GDP permette di creare oggetti di notevoli dimensioni ad alta velocità.
www.elmec.com
www.3ditaly.it
www.stratasys.com
www.massivit3d.com
www.hp.com
www.synology.com
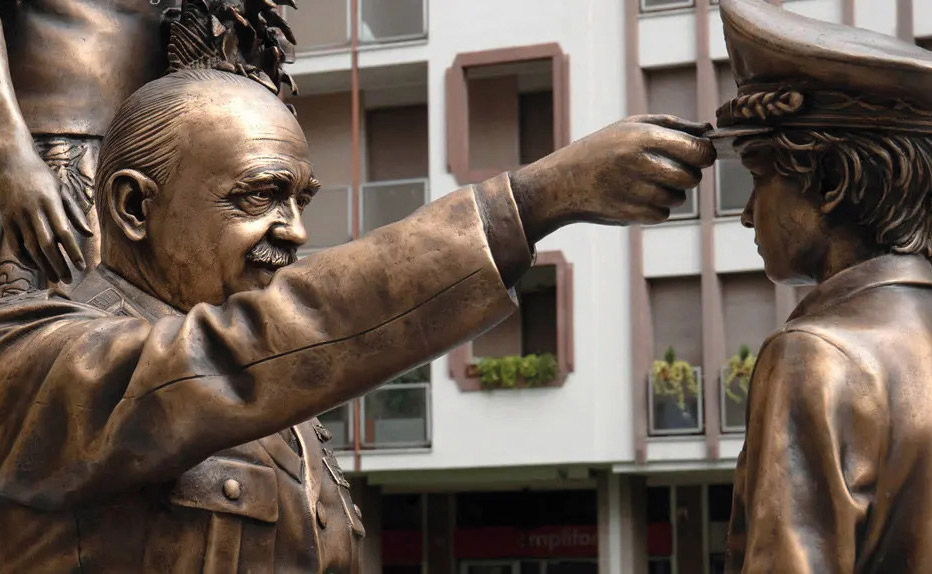
Omaggio a Dalla Chiesa
La scultura digitale fa passi da gigante. A tal punto da arrivare alla fusione di statue in bronzo direttamente dalla modellazione organica con software come ZBrush, senza passare per la scultura reale e tradizionale. Questa case history è il risultato di un lavoro a più mani iniziato dall’incontro fra Studio Dan e 3DiTALY Torino. La commissione riguarda la progettazione e la realizzazione di un monumento speciale; una fontana in ricordo di Emanuela Setti Carraro e del Generale Carlo Alberto dalla Chiesa.
La giovane sposa del Generale Carlo Alberto dalla Chiesa, Emanuela Setti Carraro, era infatti originaria di Borgosesia. L’idea di Studio Dan è quella di realizzare la fusione in bronzo direttamente dalla modellazione 3D in Zbrush delle statue, stampate poi in 3D in scala 1:1; ecco perchè si rivolge a 3DiTALY Torino, che accetta subito con entusiasmo la collaborazione.
L’opera è stata concepita dallo Studio Dan e dallo Studio di progettazione Canuto come una fontana che, vista dall’alto, ha la forma dello stemma della Repubblica Italiana. All’interno della fontana le statue del Generale Dalla Chiesa, della sua sposa Emanuela Setti Carraro e di alcuni bambini.
Le fasi:
- PROGETTAZIONE CAD. Modellazione organica delle sculture, realizzata tramite il software Zbrush.
- PROTOTIPAZIONE RAPIDA. Realizzazione prototipi di alta qualità, in scala, tramite stampa 3d SLA.
- REALIZZAZIONE MODELLI FONDIBILI. Stampa 3D dei modelli definitivi in scala reale, finalizzati per la fusione.
- FUSIONE MODELLI. Ottimizzazione e fusione a cera persa dei modelli stampati in 3d.
- REALIZZAZIONE MODELLI DEFINITIVI. Rifinitura finale dei modelli ed installazione in loco.